Volume growth smaller batches
This imposes specific requirements on the packaging process. It must be one hundred percent reliable and achievable with a carefully balanced level of automation. Biomedical producers, in particular, are confronted with this challenge. The graph illustrates the expected exponential growth of smaller batches in a biomedical company. Achieving a one hundred percent reliable high mix low volume manufacturing packaging process requires a broader perspective, encompassing not only the machinery but also logistics, processes, and costs. This article elaborates on these aspects.
In the manufacturing and packaging of small batches, careful management of the goods flow and control is essential from the outset. Without this, operators spend a significant amount of time on inspection, leading to a higher likelihood of errors.
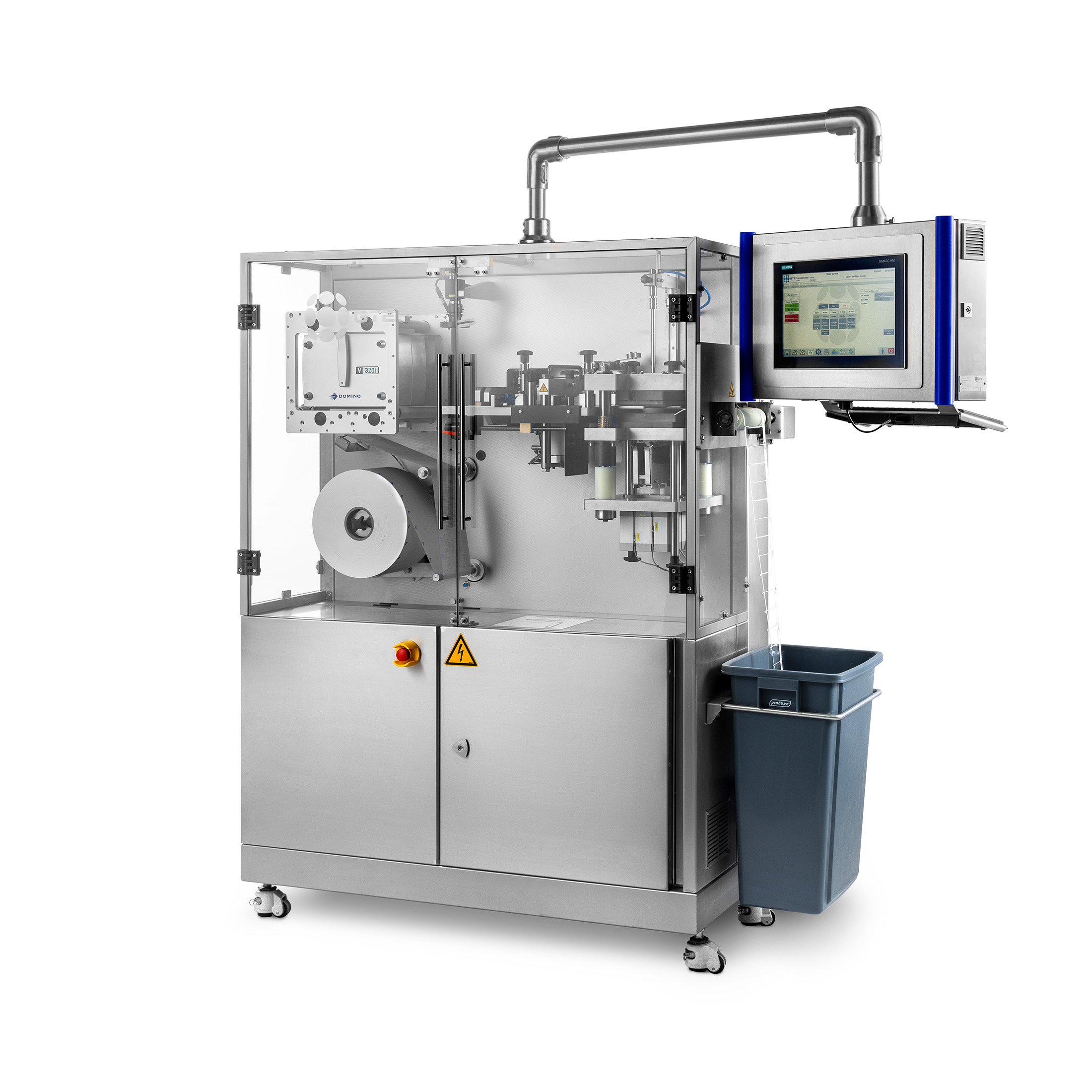
High mix low volume manufacturing and logistics
By associating a code with the batch of products and restricting access to these products solely through that code, any ‘mix-up’ is prevented. The same code is used for each process step involving that batch. Once the batch is completed, space is available for the next batch with a different, unique code. Consequently, batches are not present in the same space simultaneously. Through a robust process, operators only have access to the products when actively working on them. Other products not belonging to that batch remain inaccessible. This approach aligns well with ‘Good Manufacturing Practice’ (GMP).
Additionally, this method provides clear visibility into the flow of goods for the components. Most errors arise from operator actions and machine changeovers. These issues are mitigated through a well-defined procedure and routing. A logistical plan is crucial in the context of High Mix Low Volume Manufacturing (HMLV).
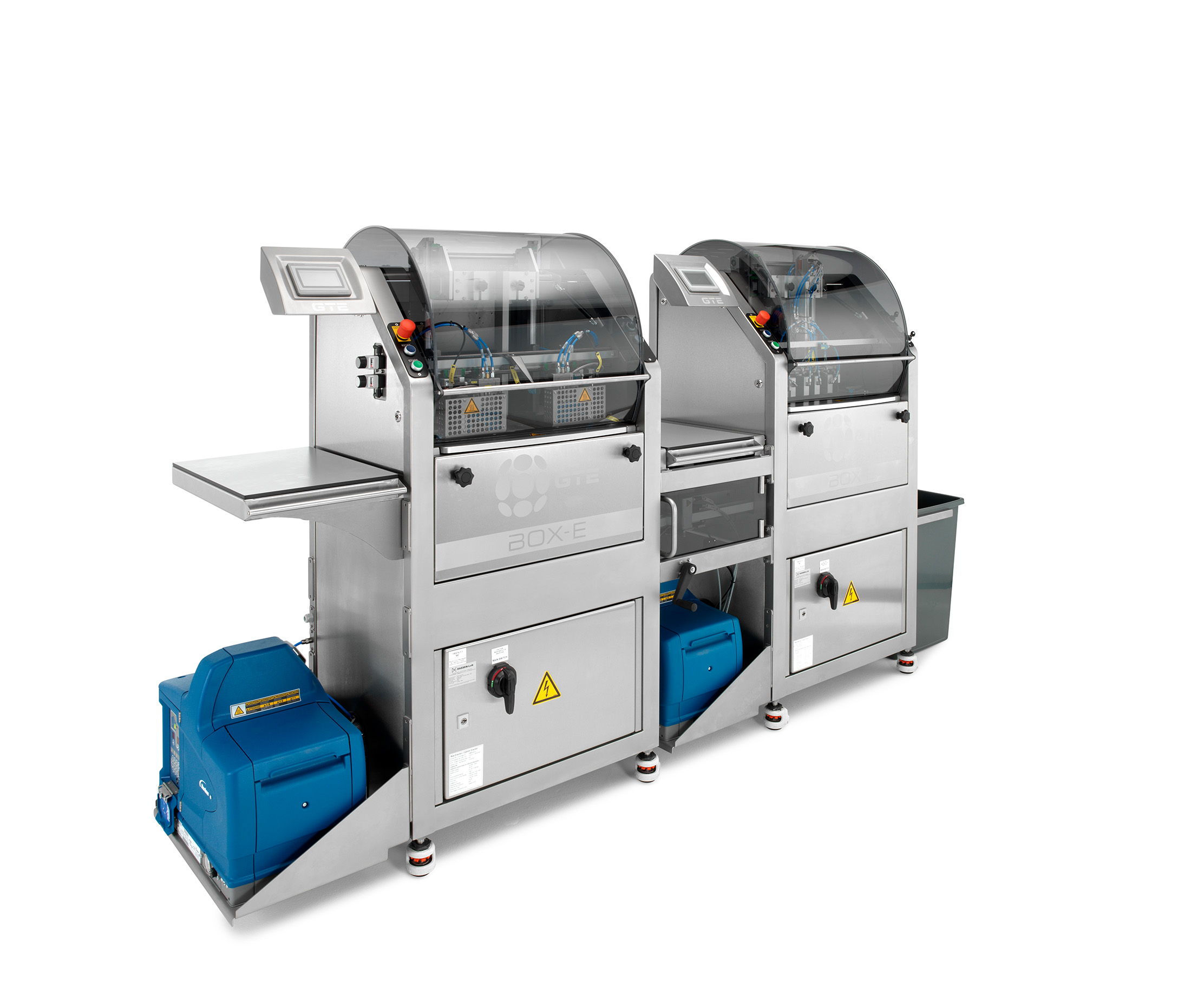
HMLV and processes
The processes that have been fully validated and set up in a high-speed machine can be seamlessly adopted in the design of the High Mix Low Volume Manufacturing machine. Each vision check and security measure implemented in the high-speed machine can also be integrated into the HMLV machine. If, in the high-speed machine, nothing can be removed after adding, for example, a syringe, but only a manual can be added, the same principle can be applied to the HMLV machine. The process is configured to ensure 100% reliability, even with the involvement of operators and more machine changeovers. In HMLV, the focus is on adopting existing techniques and safeguards from the original high-speed production line and translating them into manual or low-speed production tools with the same quality standards, safety, and validation.
Get more information
Wondering how the machine could be useful for your organisation? Request more information quickly and easily.
"*" indicates required fields
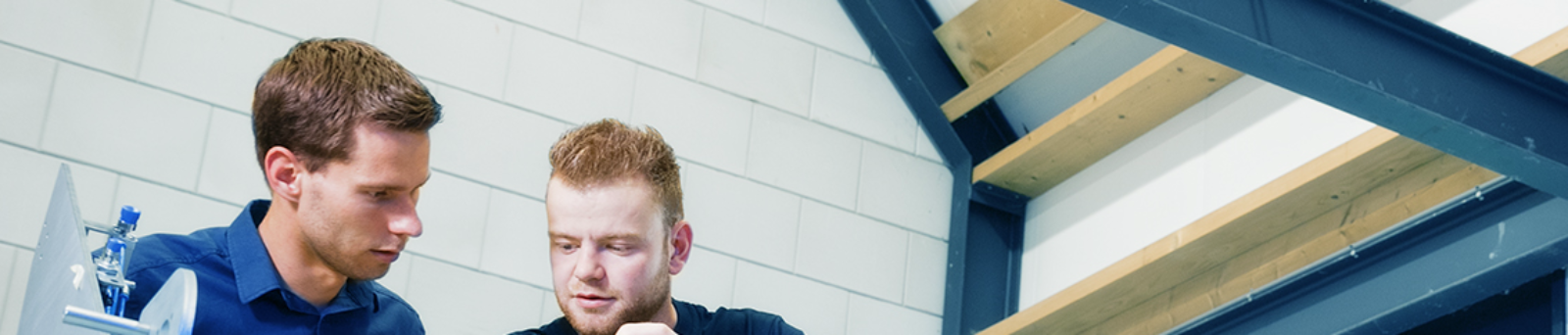
High mix low volume manufacturing and machine
We translate the techniques from the high-speed line to a manual or low-speed machine. However, we take into account additional flexibility through easily interchangeable molds and tools. The changeable parts are quickly exchangeable and designed with poka-yoke principles. Where operators are involved, avoiding human errors and ensuring safety are crucial.
In the field of machine engineering, collaborative robots, or co-bots, have existed for many years. These robots safely replace human actions, eliminating the need for machine shielding or enclosure.
The robot stops upon contact, preventing any injuries. GTE Engineering applies this principle in the construction of HMLV (High Mix – Low Volume) machines. Speed is often less critical, but interaction with an operator is paramount. The operator should be able to produce or package products easily and safely. Safety is achieved by using HMLV machines powered at low levels. They consume only the necessary energy and pose no danger to the operators, eliminating the need for shielding.
HMLV and costs
When is it advantageous to set up an high mix low volume manufacturing environment for smaller batch quantities rather than manufacturing them on a high-speed line? The answer lies in the costs and the time required. If you solely consider the time needed, the chart below illustrates that for a batch size of just over 1000 units, HMLV machines and processes become more advantageous.
If you manufacture small batches on an automatic high-speed production line, you may encounter a situation where the machine is idle for 7 hours due to changeovers and only actually produces for 1 hour.
When considering costs, factors include:
– Machine acquisition costs
– Operator costs
– Factory costs (floor space)
In the chart adjacent, the production costs for an HMLV line are lower than those for a high-speed line up to approximately 2800 units. Beyond 2800 units, the high-speed line becomes more cost-effective. These calculations can be easily performed for any product and HMLV machine or process. This provides medical companies with better insights into production time and costs, allowing decisions to be made based on these two elements.
For many companies, delving into the trend of high mix low volume manufacturing is imperative, given the exponential growth of small-batch production in the coming years. High-speed production lines are inefficient for small batches with long changeover times, especially with a wide variety of batches. By effectively setting up HMLV production, this transformation can proceed smoothly.
More information about cobots / robots for HMLV Ask advice about HMLV solutionsLet us call you back
Curious about how our solutions can be used within your organization? Request more information quickly and easily.
"*" indicates required fields
We are ready to help you!
Mercuriusplein 45971 LW Grubbenvorst (Nederland)
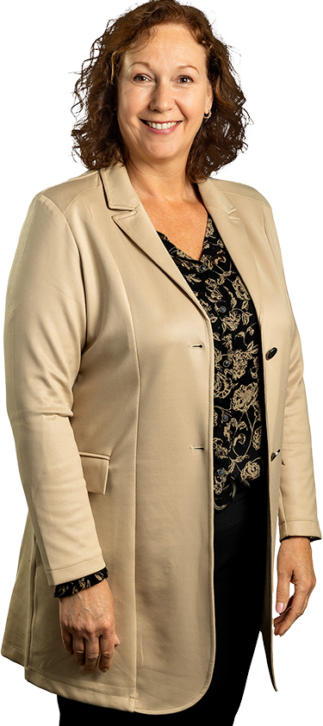
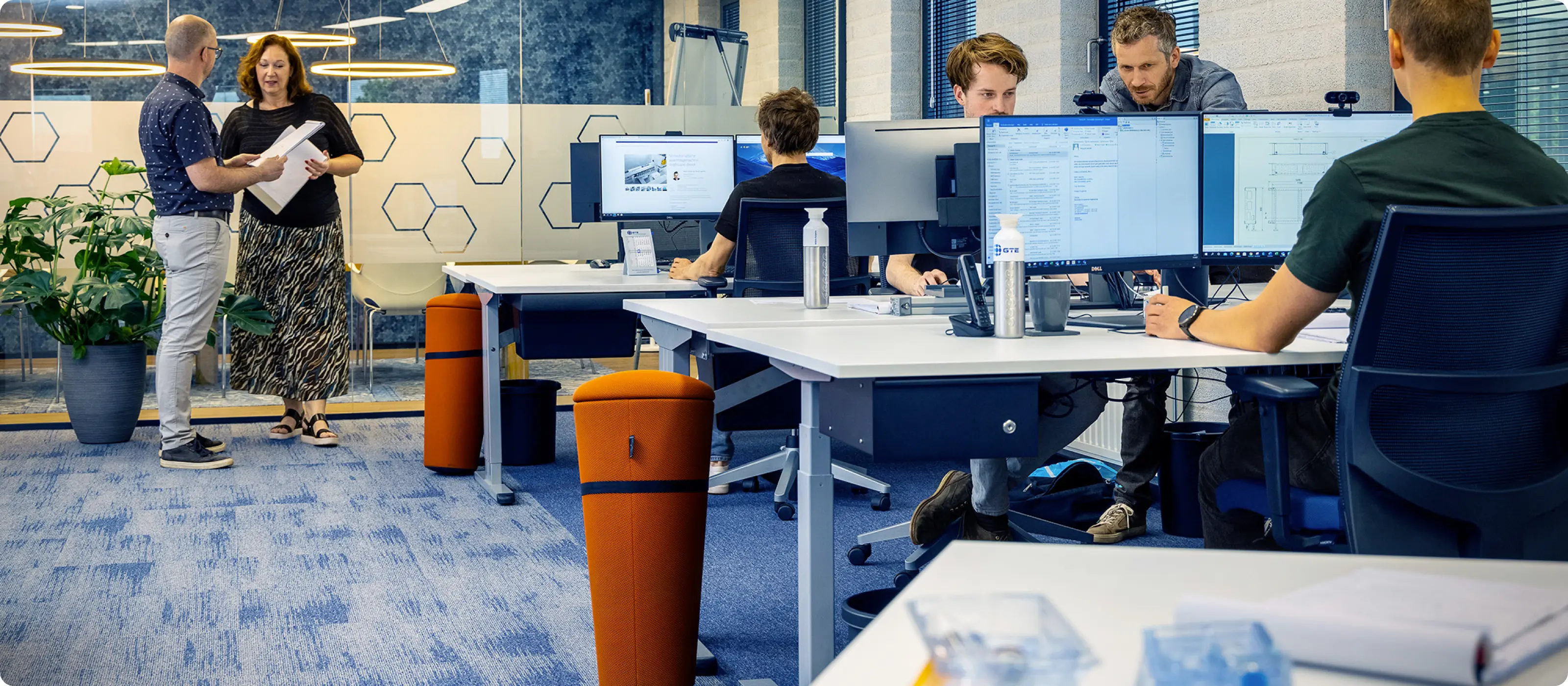