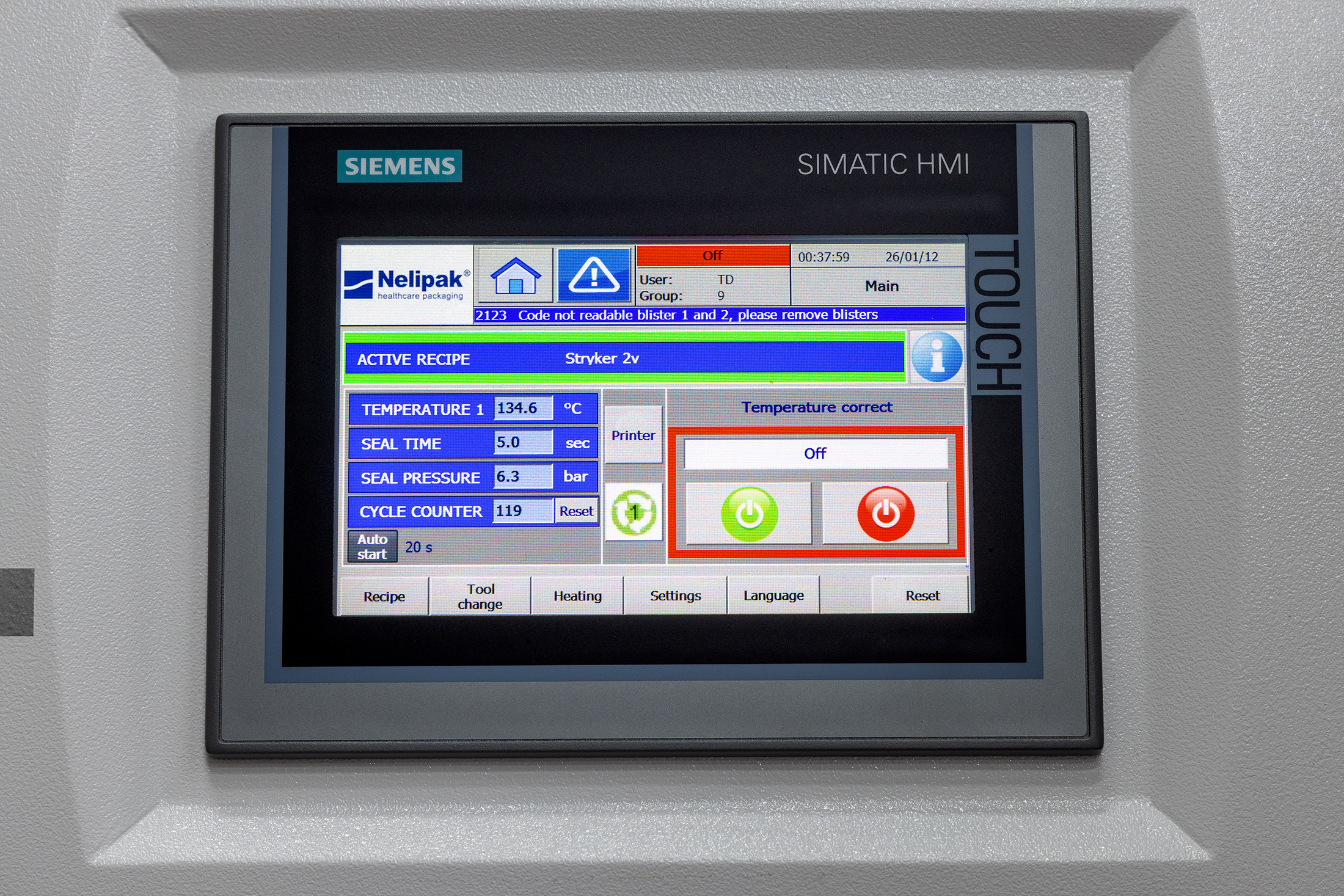
No downtime
In my view, downtime is not acceptable for production equipment. Machines can be configured to significantly boost effectiveness and efficiency. The return on investment (ROI) for these adjustments is easily calculable, providing immediate insight into their relevance for the respective companies. Often, the investment in these modifications is recouped within 1-2 years. An additional advantage is the reduction in recalls and the improvement in quality, as most errors tend to occur during downtime and machine restarts.
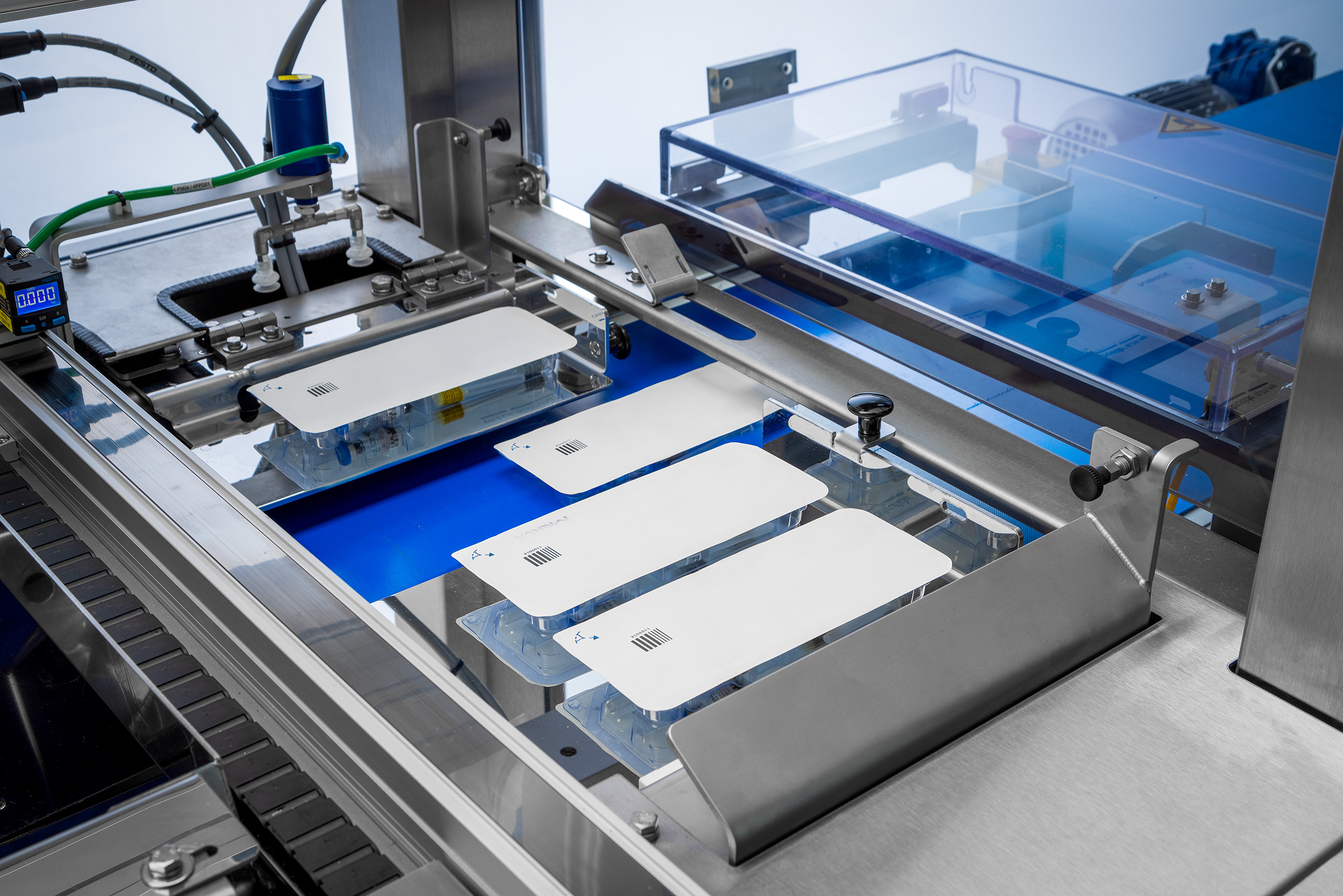
Costs Downtime
- No production
- Extra manpower
- More recalls
- More errors
- Discarding of products
- All supporting departments come to a halt
- Facilities are not utilized (power, building, light, automation, etc.)Calculation example:A machine runs for 10 hours a day and is only productive for 60% of the production time. It is idle for 40%, both planned and unplanned. This machine produces 20 products per minute, and these products cost €2 each.The revenue lost due to this downtime is €124,800 per year. These are the direct losses; the indirect losses, such as the costs of extra manpower, the costs of errors and recalls, and all other costs associated with downtime, have not even been factored in.
Get more information
Wondering how the machine could be useful for your organisation? Request more information quickly and easily.
"*" indicates required fields
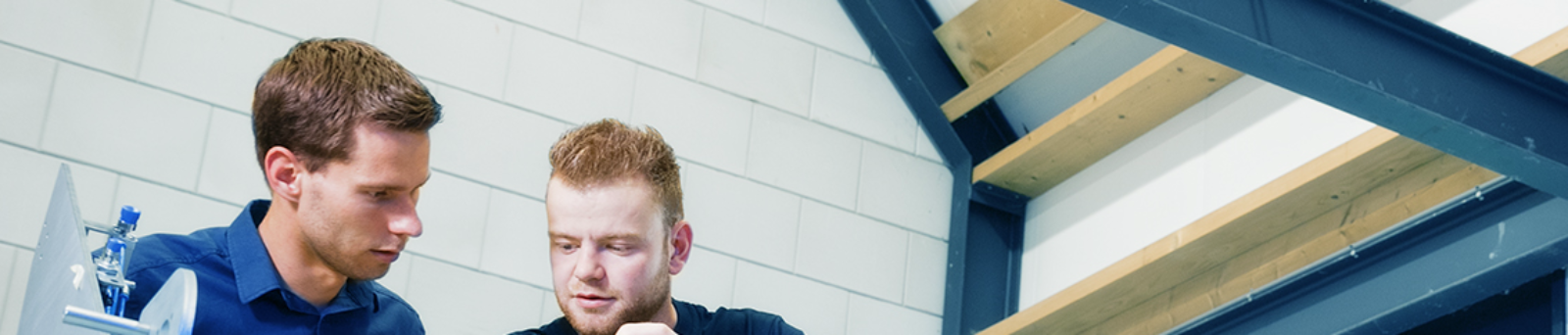
Back-up machine
What we sometimes observe is that companies attempt to address downtime by investing in a second identical machine, essentially a backup machine. This approach is not only expensive in terms of acquisition and maintenance but also introduces the same issues as the first machine. Often, components from the second machine are used in the other machine when a problem arises, rendering the second machine unusable. This approach doesn’t solve the original problems, and costs remain high during line clearance. Many errors still occur during machine downtime.
Buffering
Downtime within production lines also leads to buffering behavior. To prevent insufficient product availability, operators ensure there is stock, allowing the next component to always be available. This inventory represents idle capital and occupies unnecessary space.
A good production and packaging machine for medical and pharmacy should have a minimum efficiency rate of 90%. Only 10% (or less) of the time should be allocated to downtime, most of which is for routine maintenance. This is a standard that you can expect from your supplier of packaging and assembly machines.
We are happy to calculate the potential yield of a custom-made machine with higher reliability than your current machine.
Let us call you back
Curious about how our solutions can be used within your organization? Request more information quickly and easily.
"*" indicates required fields
We are ready to help you!
Mercuriusplein 45971 LW Grubbenvorst (Nederland)
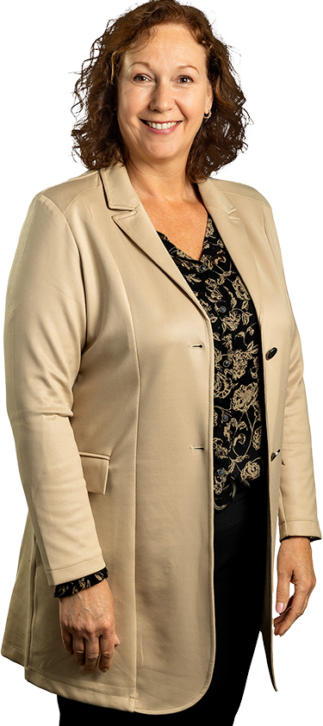
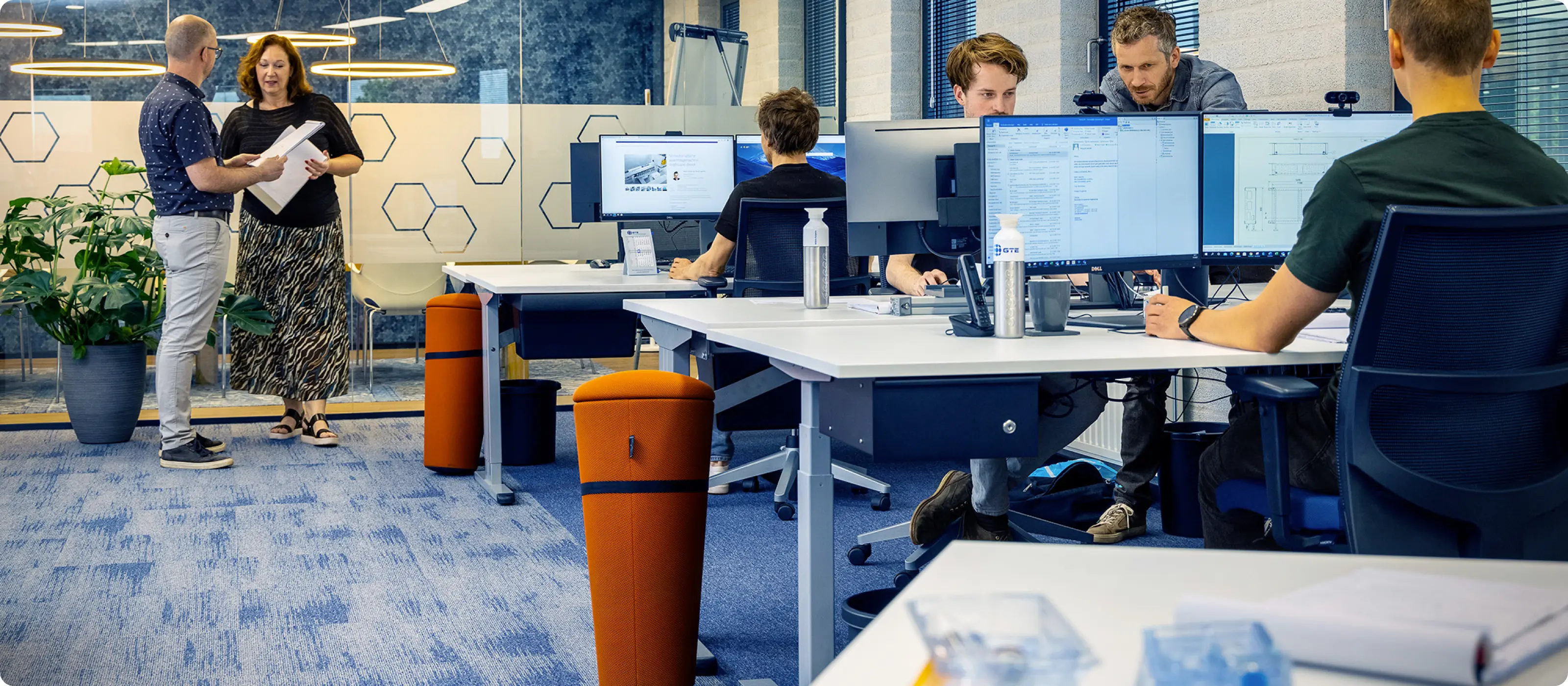