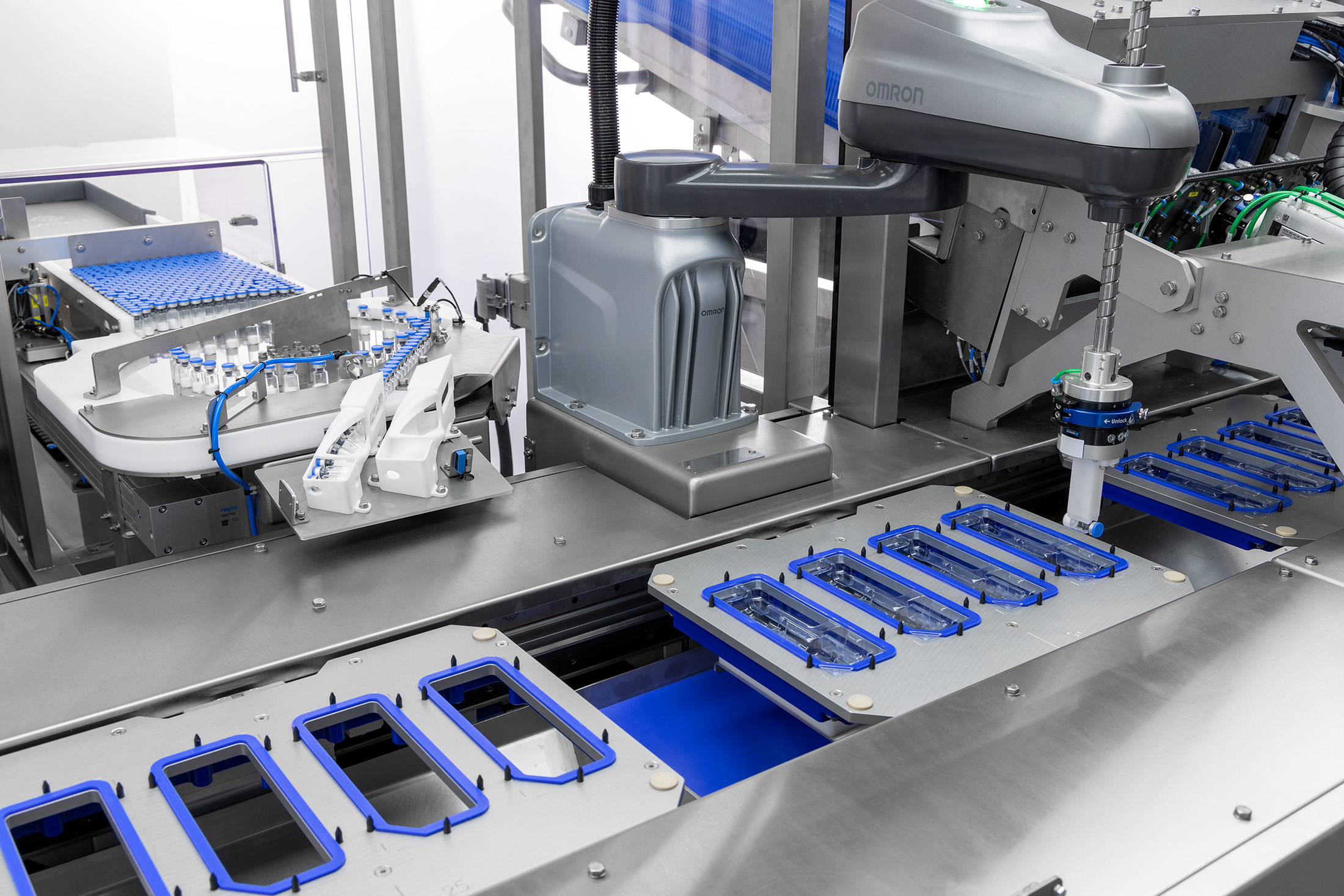
Creative process
GTE Engineering designs and constructs custom machines for the international medical and pharmaceutical industries. These machines are employed for the assembly and packaging of medical and pharmaceutical products. In the creation process of these machines, 3D printing plays a significant role.
Specific, custom-made machines are typically one-of-a-kind. Therefore, they must function correctly from the start, necessitating a comprehensive testing program. For the quick and efficient setup of a testing setup, often in the form of scale models, we utilize 3D-printed components. This approach allows us to thoroughly examine the operation of various parts and easily implement any necessary improvements.
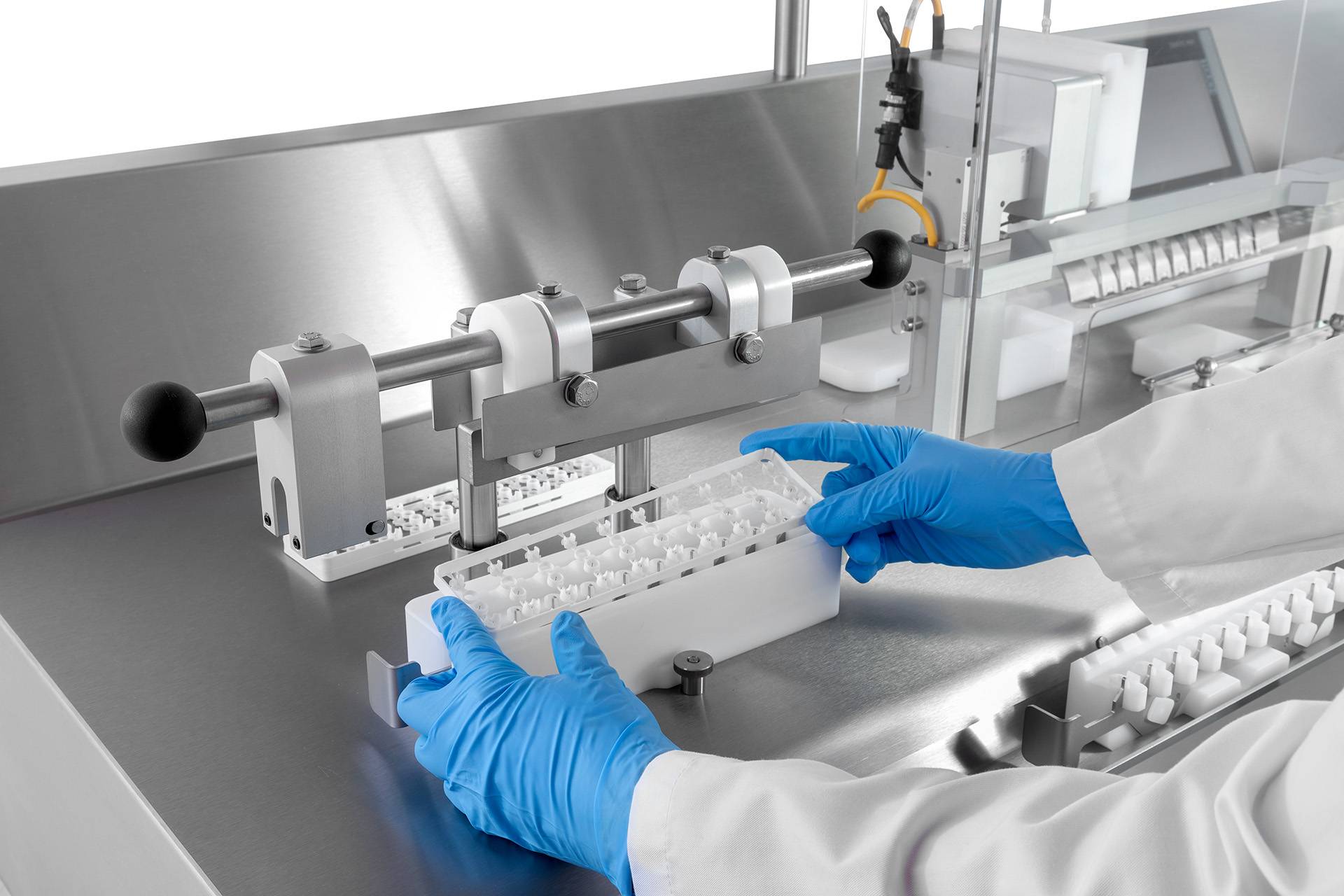
Protoypes
Larger prototypes can also be created quickly and at limited costs through 3D techniques.
Some advantages of 3D printing over conventional techniques:
- Time savings: the process from design to realization is much faster with 3D printing.
- There is no need for molds, forms, and other manufacturing aids.
- Weight reduction; printing in honeycomb structures also saves on material costs.
- Geometric freedom: curves that were conventionally impractical are now achievable. In the past, complexity meant higher costs, but with 3D printing, complexity does not impact the production cost.
- Multifunctionality: by integrating various functions, fewer components are needed, reducing assembly costs.
Get more information
Wondering how the machine could be useful for your organisation? Request more information quickly and easily.
"*" indicates required fields
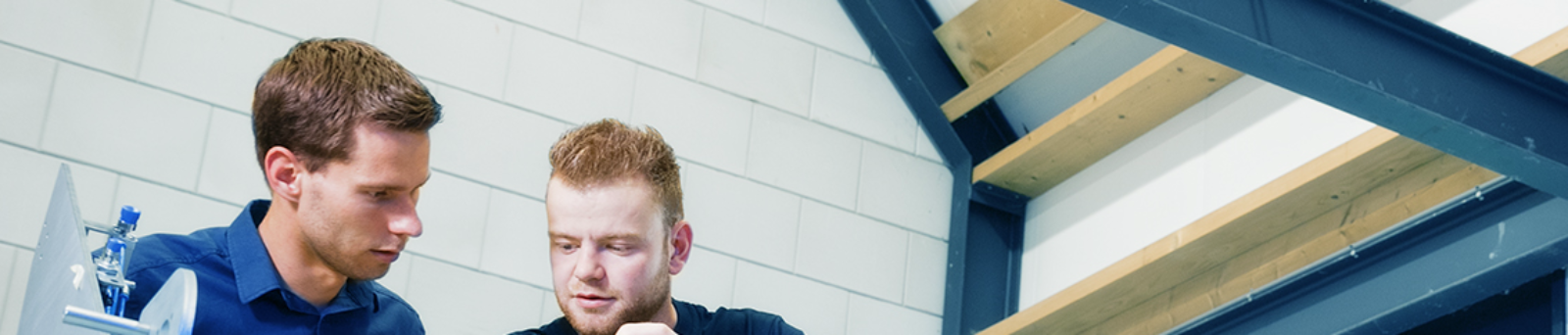
Savings in time and money
The price of 3D printing has fallen drastically in recent years and is therefore hardly an obstacle anymore. It does require a different mental attitude. Engineers must not only have knowledge of the ins and outs of the various 3D techniques and 3D file creation, they must also be able to think outside the box and trusted solutions. They must be resourceful and able to think differently. At GTE engineering we do no different. Thinking has become second nature to us.
GTE has several applications for 3D printing:
- Complex parts: cost savings and innovations.
- Testing tools: eliminating risks.
- Demonstration models: convince customers.
- Rapid prototyping: fast feedback.
There are many different 3D printer techniques. There is no one printer that solves everything for us. The extrusion technique (FDM), the stereolithography process (SLA) and selective laser sintering (SLS) are most commonly used.
3D printing will play an increasingly important role in the future and will become even more accessible and cheaper. However, it requires a different way of thinking, daring to let go of tried and tested frameworks. The limitations of other techniques no longer exist. Every conceivable shape can now be made. Making optimal use of this freedom of form will be the major challenge for the industry in the coming years. A challenge that GTE engineering feels more than at home with.